Taking the First Step Towards NDE 4.0
Part 7: Are we there yet?
No, not quite. Ultimately, NDE 4.0 is a process, not an end result.
In this series, we have discussed the concept of “NDE 3.5” as a shorthand term for some incremental steps that can be taken to get more out of your NDE process and the data that it generates.
We began by asking questions:
- What is NDE 4.0 and should we be working towards it?
- Is implementing more automation worth the effort?
- What are the potential benefits?
- Can we implement changes incrementally?
In almost every case, the answers is Yes.
Yes – it is worth investing in more automation of NDE, and yes – the benefits can be gained incrementally. Implemented individually, there is significant benefit to be gained from each of the ideas we have discussed in this series. There is also a multiplier effect: implementing ideas together mutually enhances their value. Automating any single step of the NDE process from setup to reporting provides benefits that accumulate for every stage of the process.
Automation of…
- instrument calibrations and equipment setup accelerates the process, while providing improved reliability. This helps ensure the acquisition process isset up for success.
- data acquisition improves speed and ensures the repeatability of the process, thus ensuring consistent quality of the inspection data.
- analysis increases the productivity of expert human analysts, and allows NDE to keep pace with manufacturing. Automated analysis requires consistent inputs with a high quality of data.
- reporting enables one inspection to serve many audiences beyond the NDE and quality assurance experts. NDE information can be made accessible both upstream to process engineering, and downstream to product life cycle management and in-service inspection teams.
Documentation of the configuration and outputs for any step can be automatically embedded in the record of inspection. Embedding additional metadata such as the identity of the item, its location, and other contextual information enables further insights through analysis of aggregated data from many inspections of many items.
Implemented all together, these innovations position NDE systems and their processes to fit within a wider ecosystem of manufacturing, maintenance and repair of a product throughout its entire life cycle.
However, this sophisticated state is still not NDE 4.0.
Recall that NDE 3.0 involves a process of digitization: analog sensor data is digitized, then stored, evaluated and shared digitally. NDE4.0 involves digitalization where multiple digital technologies – both within and outside of the NDE process – are interconnected into an ecosystem of cyber-physical systems.
In the NDE 4.0 environment, the inspected items and the NDE process equipment have digital twins, which represent the physical items and processes in a virtual environment. The NDE process can be influenced by information and decisions from outside the NDE system, and data created by theNDE system is used to produce insight which influences processes and decisions well beyond the NDE process. Digitalization is about the interconnectedness of information and decision making between systems, a feedback and value creation loop, not just shared access to data.
For even the most sophisticated organizations, there are still significant challenges to overcome, as discussed by the originators of theNDE 4.0 discussion.[1] For example, in 2023, we do not yet have universally accessible shared formats for NDE data, although several efforts are under way. We also do not have well defined interfaces for NDE equipment to interact with other digital systems in manufacturing, maintenance and information technology. Development and widespread acceptance of these interfaces is necessary for any NDE process in manufacturing or in-service inspection, to achieve an NDE 4.0 level of integration and the benefits thereof.
Few of us are yet at NDE 4.0, and we may never need to get all the way there. Nevertheless, taking the incremental steps to prepare for the imminent future will be beneficial.
The inverse of this premise is that not preparing – as in taking no steps – to improve an existing NDE process is likely to be detrimental to company processes as well as to the bottom line.
Automation and digitalization are rapidly increasing in every aspect of modern life. Industries where NDE has a significant role, such as advanced manufacturing and asset maintenance are no different. Innovation and continuous improvement of all processes are requirements for any business to thrive in a rapidly changing and competitive environment.
Welcome to NDE 3.5. Keep going, and keep up the good work.
Want more NDE 4.0? Here are some useful resources:
- Singh, Ripi; Vrana, Johannes, The World of NDE 4.0, 2022, American Society for Nondestructive Testing, Columbus OH.
- NDE 4.0 Channel on Youtube
- Inspiring Next
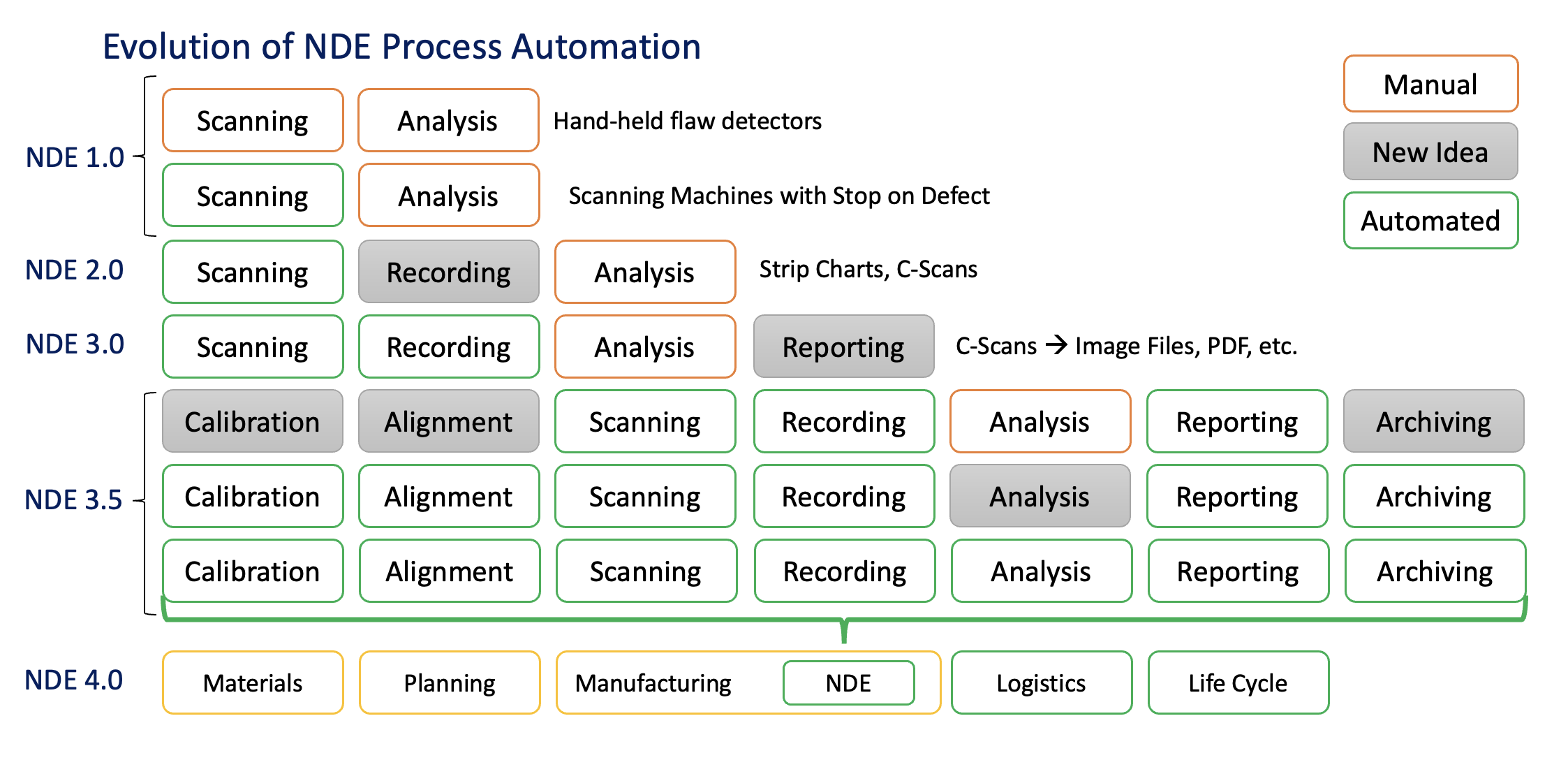
Image adapted from: W. Weber, D. Mair, D. Jansen, L. Lombardi , ’Advances in Inspection Automation’
QNDE Proceedings, 2009
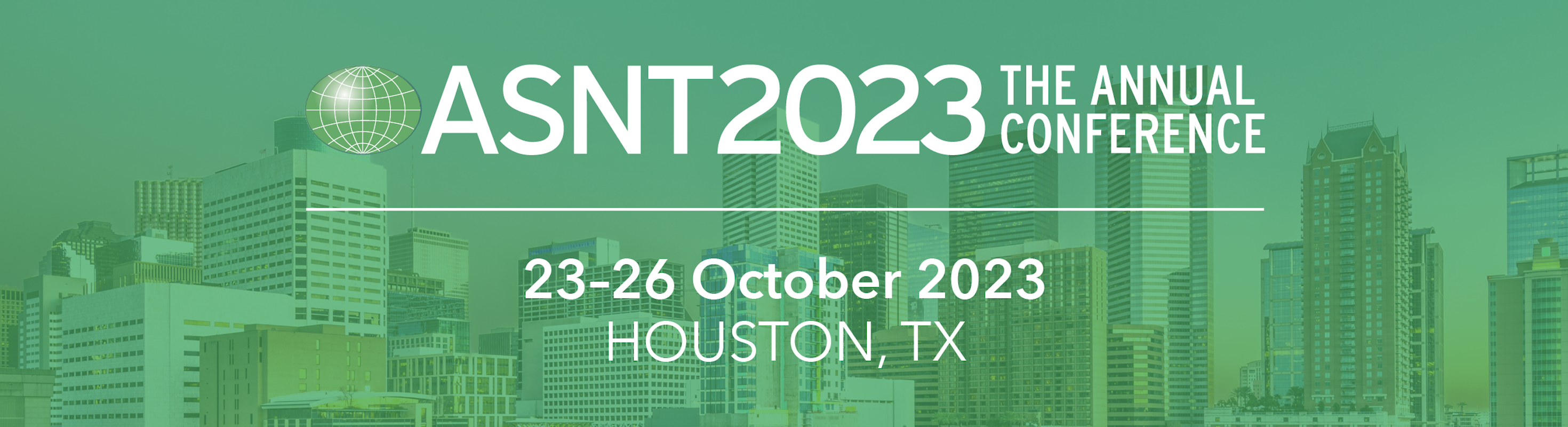
UTEX is attending the ASNT Annual Conference in October. Want to chat about NDE 3.5, our instruments, or your NDE challenges, reach out to set up a meeting. Is that too long to wait, contact us to meet up sooner.
More in "Taking the First Step Towards NDE 4.0" series
|