Taking the First Step Towards NDE 4.0
Part 4: Automated Analysis of NDE Data
There are pressures to automate ever more complex NDE systems: process speeds are increasing, demographics are changing in the NDE workforce with attrition of the skilled workforce, and clients have increasing expectations to have more data - and more metadata - about their manufactured products. In this fourth article on the topic of NDEAutomation, we will discuss the automation of NDE data analysis, which is the next step in the automation process after automating data collection. We will also discuss the importance of metadata for automated analysis and how it helps integrate the NDE process into the larger manufacturing environment. Our last post discussed the increasing importance of metadata (data about yourNDE data) for nondestructive testing systems. Metadata is an essential pre-requisite for automating the analysis ofNDE data.
The post also explains why automated analysis is necessary and how it works.
What is Automated Analysis?
In our discussion, automated analysis occurs within the context of a manufacturing process: objects to be inspected will arrive at the NDE machine, where they will be scanned. The resulting inspection data will be evaluated against a set of rules, and a decision to accept or reject the item will be rendered. The Accept / Reject decision may then be communicated to a factory materials management system. All of this occurs without human analysis or intervention as part of a closed feedback loop.
Advancements in NDE instruments, software, and computing power have enabled automation of many NDE applications that have previously required trained human inspectors and analysts. There is a beneficial complementary effect at work: the analysis must be automated to keep up with the automated scanning, but the analysis can only be automated because the data collection is itself already automated. Automated inspection produces data that is consistent in its quality and presentation, so that the data is ready for analysis without any further amendment, sorting, or pre-processing.
The analysis algorithm need not be any more sophisticated than the existing methods used by human analysts. In fact, because humans have to define, validate, and approve these automated methods, the automated analysis algorithms are usually based upon the same rules that a human analyst would follow. Regulatory standards and customer specifications will typically define an easily automated set of criteria for what constitutes a reportable or a rejectable indication. Any such indication found within the data will be automatically tabulated and measured by the software, and the decision to accept or reject the item will be rendered on the basis of the rules for allowable size, allowable location, and so on. The automation of the process provides vastly greater speed than a human, with greater repeatability.
Why metadata is needed:
Truly automated analysis is more than just the process of parsing a dataset and making a decision based upon rules. That decision making step occurs in the middle of a larger series of data management and reporting steps.Those preceding and following steps are where the NDE metadata earns its value, enabling the software platform to integrate data acquisition, data analysis, decision making, and NDE process management within the context of the larger manufacturing environment.
Among its many uses, the metadata is used to track the following as it pertains to a manufactured item:
- Classification
- Identification
- Status
Classification: the automated NDE system needs to know what is coming down the conveyor, or what has been grasped by the robot arm. The classification of an item defines how the NDE machine should handle the item and present it to the sensors for inspection. This classification also enables the NDE software to lookup the correct inspection configuration for that item, then load the inspection instrument accordingly. Finally, this classification enables the analysis software to look up and apply the appropriate rules for evaluating the data from the automated scan.
Identification: All modern manufacturing tracks products with some form of identity code. This may be a date and time, a batch number, or a serial number, in the case of high value items. The identity information enables the analysis software to report which product is acceptable and which is rejected. The management of the manufacturing process depends upon this information. If products are being rejected frequently, then there is a high probability that something may be wrong with the incoming material or the manufacturing process, or both.
Status: A manufactured item will pass through at least three changes of status during an automated inspection: Not Inspected, Inspection in Progress, and Analyzed & Accepted or Analyzed & Rejected. The automated analysis software must be capable of alerting the process control system that the item has been rejected. The software should also be able to apply a metadata tag to the NDE data file, so that it is easy to trace those data files which have caused a rejection of the inspected item.
How is Automated Analysis Delivered?
A team effort is needed to deliver and manage a fully automated NDE system. Manufacturing automation engineers, who have expertise in high speed, precision handling of manufactured items, need to work closely with the NDE experts, who understand the requirements of the inspection process, and with the information technology specialists who can integrate the NDE process with the rest of the information flow for the manufacturing process, or even the entire factory.
Factory automation controllers and process control software do not integrate directly with nondestructive test instruments. NDT instruments that have been designed for human operation are not capable of direct integration within a factory automation ecosystem either. NDE software, that is specifically geared towards automation, is therefore needed to bridge the two.
The automated analysis software needs to be designed with the human NDE expert in mind, since it is they who will program the rules for how the analysis will take place.
Finally, the analysis software needs to have tools for exporting the analysis results and metadata to the factory quality control database. This means that an interface for the information systems expert must be provided.
The following is an example of how NDE data analysis automation can be integrated into the manufacturing process through the use of NDE automation software.
Example 1:
Precision forged rings are used in many applications such as roller bearings for railway axles, aircraft engines, and power generation equipment. They are produced in fully automated factories, at a rapid tempo. In this example, the forged and heat-treated rings undergo 100% inspection with ultrasonicC-Scans, eddy current, and sometimes visual inspection as well. For the ultrasonic inspection, the forgings must be scanned with a fine image resolution, the data analyzed, and a decision rendered within 60 seconds or less.
The ultrasonic data is full waveform capture for 3-dimensional coverage through the entire volume of the forging.
There are two regions of interest: the functional zone, which is the heat-treated working surface, and then the interior zone – the volume of annealed material underneath the working surface. Because the parts handling and scanning processes are precisely automated, the ultrasonic data that the instrument collects are consistent. This enables immediate analysis using a relatively simple detection and classification algorithm that is based upon traditional amplitude over baseline criteria.
The 3-dimensional data is gated (sliced) in the thickness dimension, to discern between the functional zone and the interior zone. Two separate analyses are conducted because the functional zone has a much lower tolerance for defects than the interior zone.
All indications are tabulated and classified according to their location. Any single rejectable indication will trigger the Reject response, which alerts the machine to divert this component into quarantine, away from the rest of the acceptable product.
A new record is automatically appended to the production quality database.
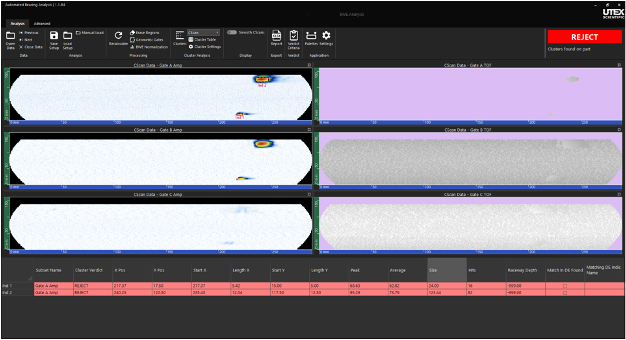
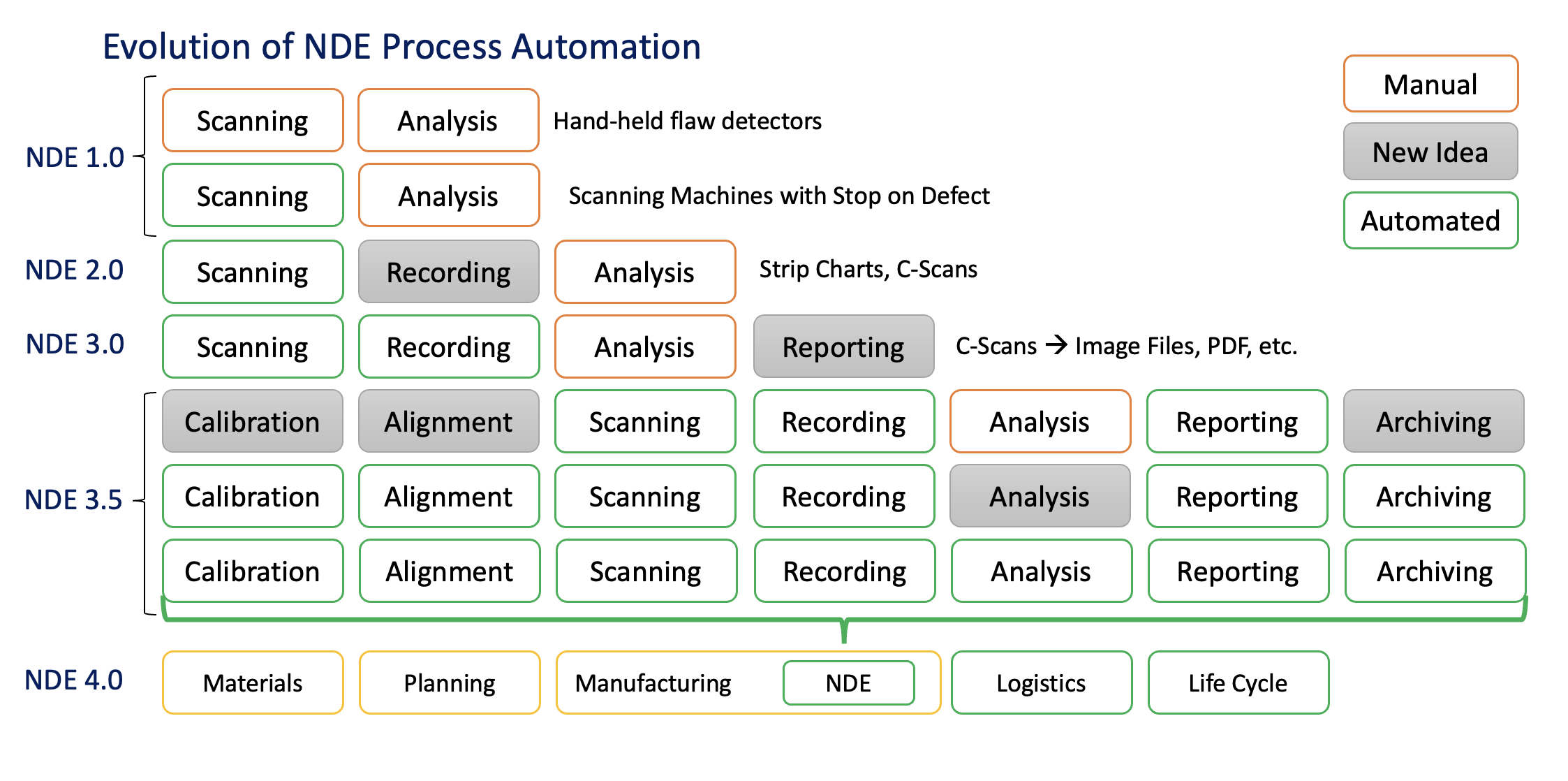
Image adapted from: W. Weber, D. Mair, D. Jansen, L. Lombardi , ’Advances in Inspection Automation’
QNDE Proceedings, 2009
Our next post will explore how reporting of analysis results can be automated.
ICYMI - Quality Magazine spoke to UTEX’s Dave Seto about Successful Automation and NDT. Listen here.
More in "Taking the First Step Towards NDE 4.0" series
|