Taking the First Step Towards NDE 4.0
Part 1: NDE 3.5 - Incremental Steps toward Greater Automation of NDE
NDE 4.0 has been a topic of enthusiastic conversation at NDE conferences for several years now. It describes the integration of a number of technologies including automation and process control, augmented reality, digital twins, AI, and machine learning. Broadly, NDE 4.0 refers to the integration of NDE processes within corporate and even global levels of data management and resource planning.
An increasing amount of automation and integration is already visible in many sectors of the NDE community, and the benefits are manifest. Nevertheless, it can be confusing or even daunting to think about all of the implications of the emerging future that we have been calling NDE 4.0.
In the evolution of NDE processes, many inspections are still operating in an analog (NDE 2.0) way. Some have automated and digitized portions of their NDE processes, but not integrated them with the factory, which can be called NDE 3.0.
But getting from NDE 3.0 to NDE 4.0 brings up a lot of questions.
- How should we approach a greater level of automation and integration, if at all?
- What are the benefits of doing so?
- What kind of investment is needed in terms of time and money?
- Is making progress towards NDE 4.0 an all or nothing proposition?
The answers to these questions are complicated and often nuanced. There is not one defined path to get there.
In this series of posts, we offer some ways to think about “NDE 3.5” or rather, the incremental steps between the current state of your NDE systems and processes, and the potential NDE 4.0 future. There are some realistic opportunities for higher levels of automation and integration. The benefits that can come from this kind of implementation can be significant, even if a full NDE 4.0 level of integration is not the end goal.
Today, we are exploring the reasons to incorporate NDE automation and where it can be introduced into approved processes.
Recent events revealing decades of inspection reports being falsified highlight the need for more automation to help detect and eliminate mistakes and fraud. If the NDE process in this most recent example had been built into the manufacturing process through automation, the falsifying of the records would have been much more difficult and provided a barrier to, in this case, reckless disregard for public safety.
NDE 2.0 analog methods of testing and paper record keeping are becoming inadequate. NDE 3.0 has digital images on local disc drives, but no database integration and no integration with manufacturing systems like MRP / ERP. All of this results in poor traceability and no true audit capability.
But how do we get from NDE 2.0 to NDE 3.0 and beyond?
Realistically, doing so is not a step function but instead an evolutionary process. A well thought out roadmap that allows for an interactive process of introduction of a new automated segment, allowing for integration of that segment into the overall process, refinement thereof, and then introduction of the next automation segment. An example of such a process can be found below.
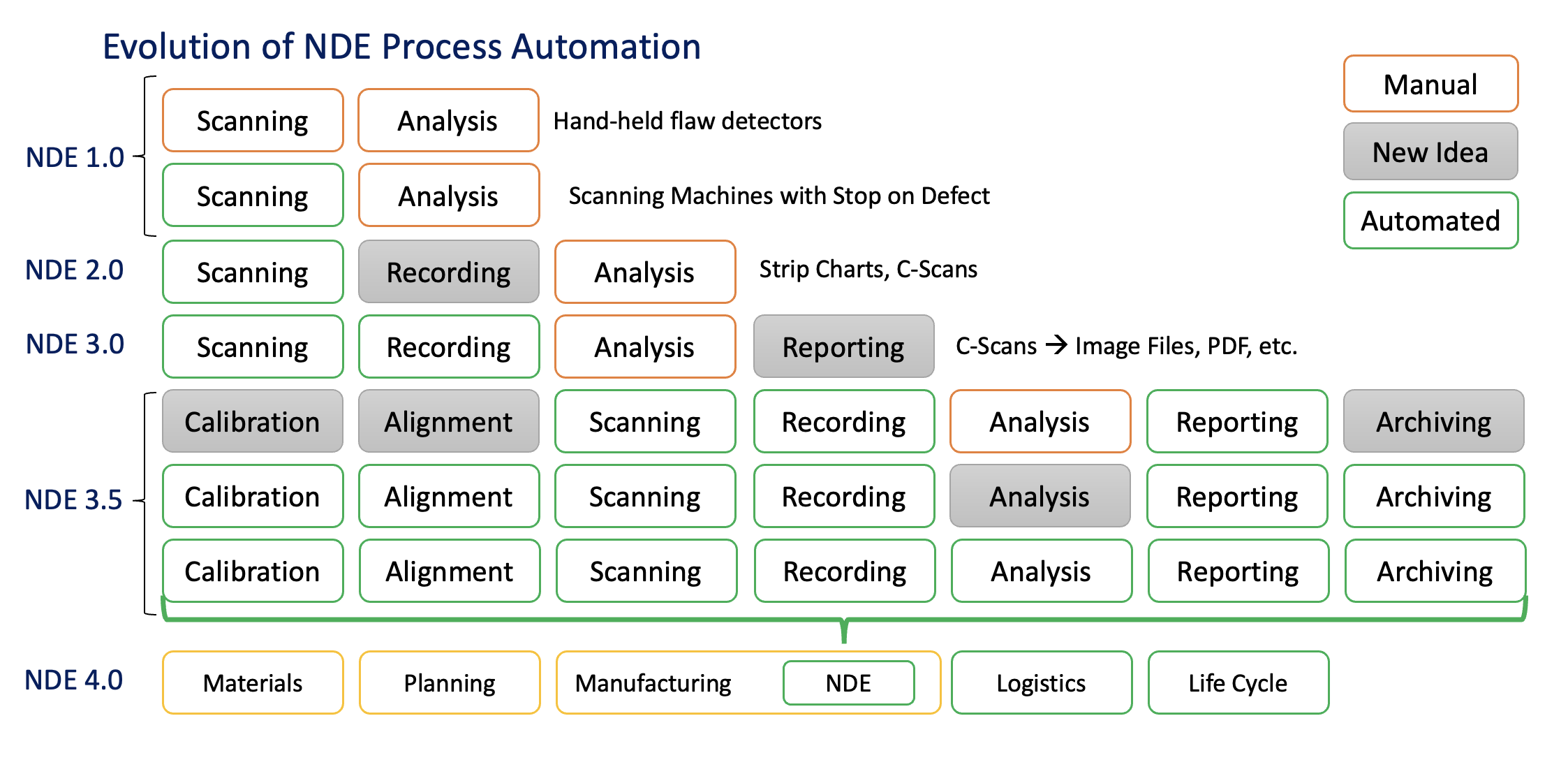
Image adapted from: W. Weber, D. Mair, D. Jansen, L. Lombardi , ’Advances in Inspection Automation’
QNDE Proceedings, 2009
Our next post will explore how introduction of these segments can be realistically achieved while minimizing impact to the approved processes already in place.
More in "Taking the First Step Towards NDE 4.0" series
|